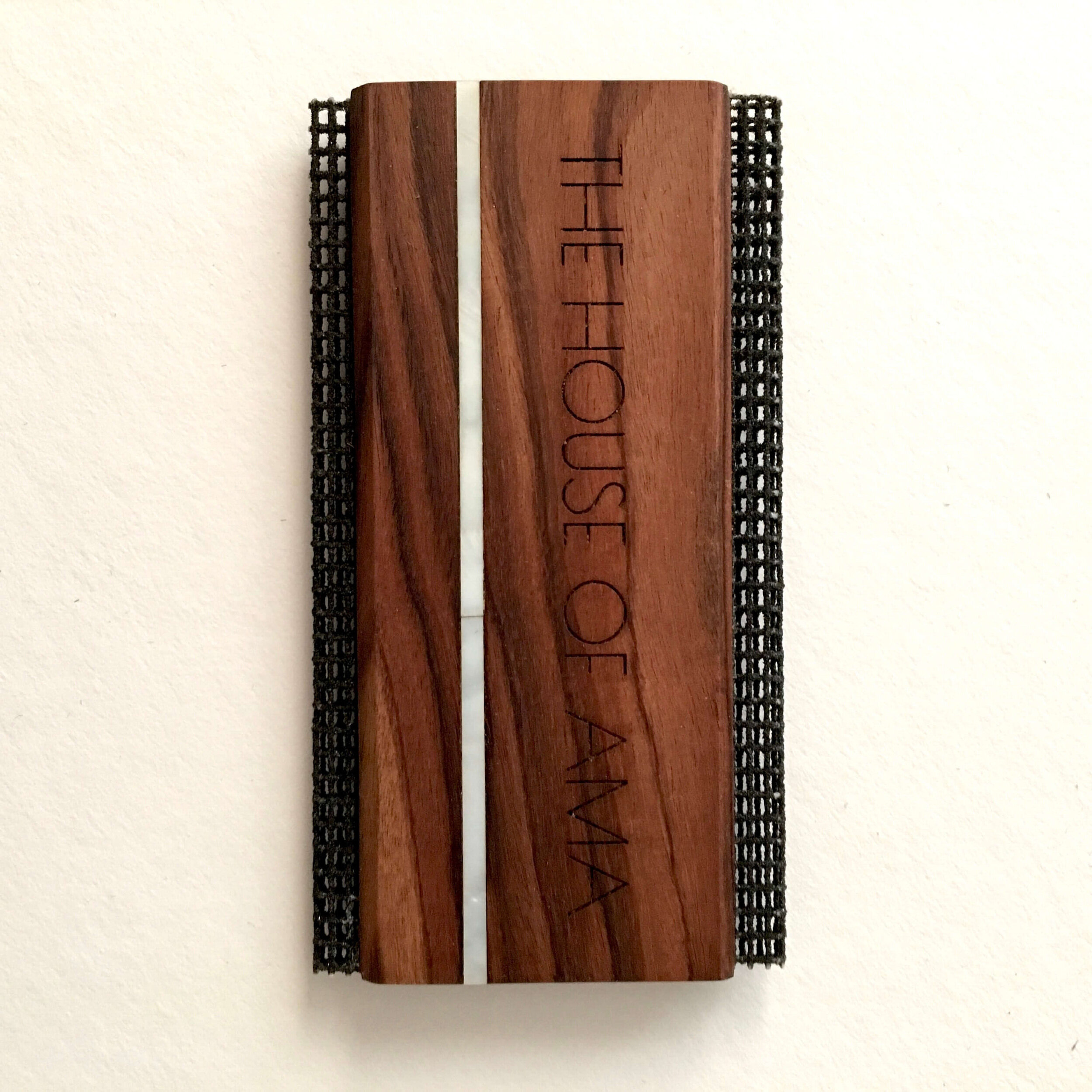
The Making
of a Sweater Comb
Some years ago, I happened upon a curious little item hanging out near the register at J.Crew . In partnership with The Laundress, an excellent company that still offers the product to this day, it was labelled as being a sweater comb, made of a pretty wood and some material on the edges I couldn’t quite discern. I decided to go for it and added one to my purchase. I am so glad I did. That little comb got a lot of action and helped me recover a ton of sweaters and other knits. There were no instructions that I recall, and I certainly wasn’t hunting for tutorials online at the time, so I just figured out how to use it with trial and error. There is possibly nothing more rewarding than watching pills and fuzz that have developed on your sweater be collected by a few firm strokes with this tool.
Quite a few years later, while engaged in my exquisite material vintage collection THE HOUSE OF AMA, I was approached by a dear and very sustainably-minded friend who was working for a company that made products out of exotic woods and was searching for ways to save the post-production scraps from being discarded.
“Just imagine what we could make from English Yew, Ebony, Rosewood, or even Kingswood!”
And imagine I did. An image of a gorgeous exotic wood sweater comb came to mind and so I immediately pitched it.
Not surprisingly, he promptly asked me what a sweater comb was.
On our next meeting I brought my comb for show as a potential subject for our project, but there was only one problem, I had no idea what the material that captured the fiber was made of. We decided to sacrifice my comb and pull it apart so that we could analyze it. Stumped, I had initially thought it was a nail emery board of some sort because it had a similar gritty texture, but we eventually came to the conclusion that it was just drywall sanding screen. We even identified the light markings on the screen that looked like product numbers, and lo and behold, when we bought a package of screens they had that same kind of marking.
So now we had our two components, wood and drywall screen. Using the J.Crew comb as an example, Mark went to task determining dimensions, and how best to produce the side groove carve-out for the screen. He tested various glues to securely join them together. We made many variations, testing different grades of screen to find out which one best collected the fibers without being too harsh and which allowed the user to easily remove the collected fuzz. We played with finding the perfect width of screen so that it would not bend with use, but was still forgiving enough not to harm the garment.
Once we had our specs, we were able to concentrate on the look and finish. We tried different levels of sanding and cures and eventually settled on sanding to the point where it was buttery smooth but still had a bit of surface texture to help with grip, and a natural beeswax finish to keep the beauty of the wood the focal point. We also added a of mother of pearl inlay, a nod to a branding motif of my business, and laser engraved the collection name.
And here they are.
Our first successful batch of reclaimed exotic wood sweater combs:
I brought them to events and sold out right away. Truly a limited edition, we had the opportunity to make just a few more batches. I have hung onto a few for safekeeping and use the one I claimed for myself regularly and when doing demonstrations. I am happy to report that it has held up exceptionally well - kudos to Mark!